Oriel STAT A MATRIX leverages a proven approach for QMS implementation and development that combines planning, training, and follow-up consultation to ensure all activities related to a successful quality system are effectively and efficiently implemented as well as sustainable.
For established companies, our 14-Step Quality Management System Implementation and Certification Program provides a framework to develop or harmonize systems that meet FDA and/or ISO 13485 requirements.
For companies that are in the early stage of product development, our “Quick-Start” QMS Development Program – which is often initiated as part of a 510(k) regulatory strategy – considers the cash flow and workload realities of a smaller company by focusing on establishing the QMS elements that are appropriate for your current manufacturing needs. In this approach, the QMS is designed to evolve as your company matures.
Two-Phase Approach for QMS Implementation
Phase I: Phase I of the Quick Start and 14-Step Programs is focused on providing you with an understanding of your current level of compliance, showing you where there are opportunities for improvement, and developing an Action Plan for moving forward with certification/compliance. Upon conclusion of Phase I, management will have the information needed to make an informed assessment of the amount of time and resources required to attain certification/compliance.
Phase II: During Phase II, the Action Plan developed in Phase I is implemented.
The process flowchart below illustrates the Oriel STAT A MATRIX Quality Management System Certification Program.
For the full 14-Step Program, Phase I includes Steps 1-3 and Phase II includes Steps 4-14. For our Quick-Start QMS Development Program, we follow a simplified model that is similar in spirit.
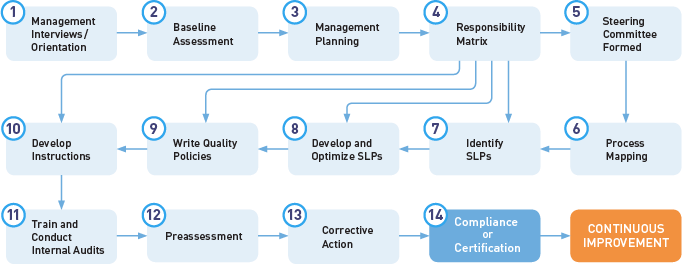
Why Choose Oriel STAT A MATRIX?
We have assisted thousands of organizations in attaining certification to ISO 9000 and related standards such as ISO 13485 and FDA’s QSR.
What distinguishes our approach is our focus on both performance and conformance. We use the certification process as an opportunity to analyze your processes with the goal of improving them before they are standardized and documented. While this approach may take slightly longer than others, the small investment of time will yield opportunities to improve organizational performance. These recommendations provide a tangible ROI for the initiative, ultimately improving shareholder value and customer satisfaction.
Contact us to learn more or for a quote.